When it comes to hoses, the material you choose can make a big difference in performance and longevity. Silicone and rubber hoses are the two most common options, and each has its own pros and cons. This guide will help you understand the differences between silicone and rubber hoses so you can make an informed decision for your business.
Silicone hoses are better than rubber hoses because they can handle more heat, last longer, and are more durable. While rubber hoses are great for a lot of things, silicone hoses are better for high temperature, flexibility, and a bunch of other industrial and automotive applications.
Now, let’s go into more detail about the materials, properties, pros, cons, and applications of silicone and rubber hoses.
What Are Silicone Hoses Made Of?
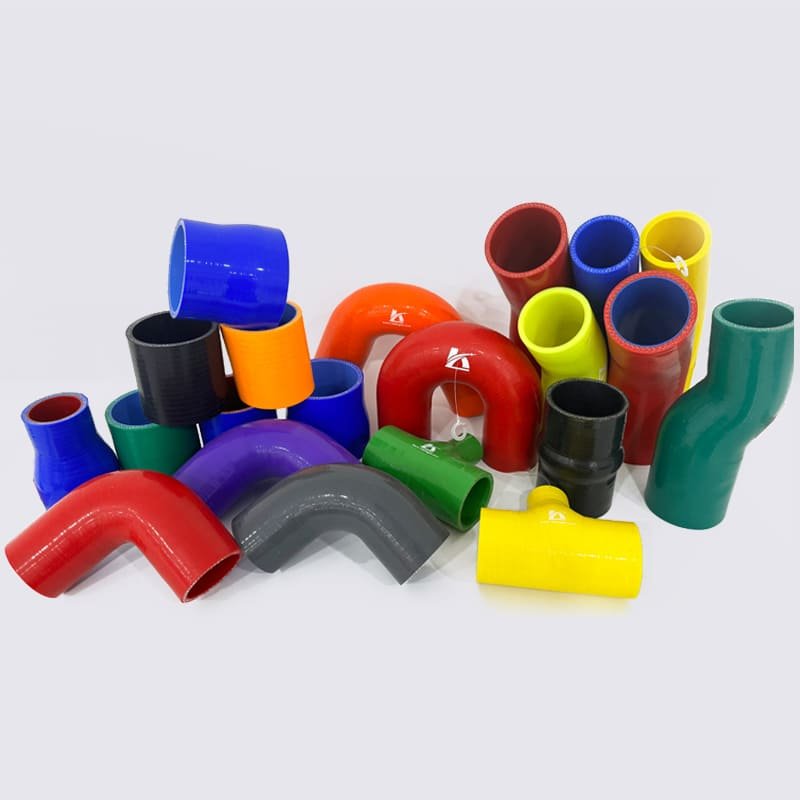
Silicone hoses are made from a synthetic polymer called silicone rubber. It is known for its heat resistance, flexibility, and durability. Often, this material is reinforced with polyester or aramid fibers to make it stronger and perform better.
What Are Rubber Hoses Made Of?
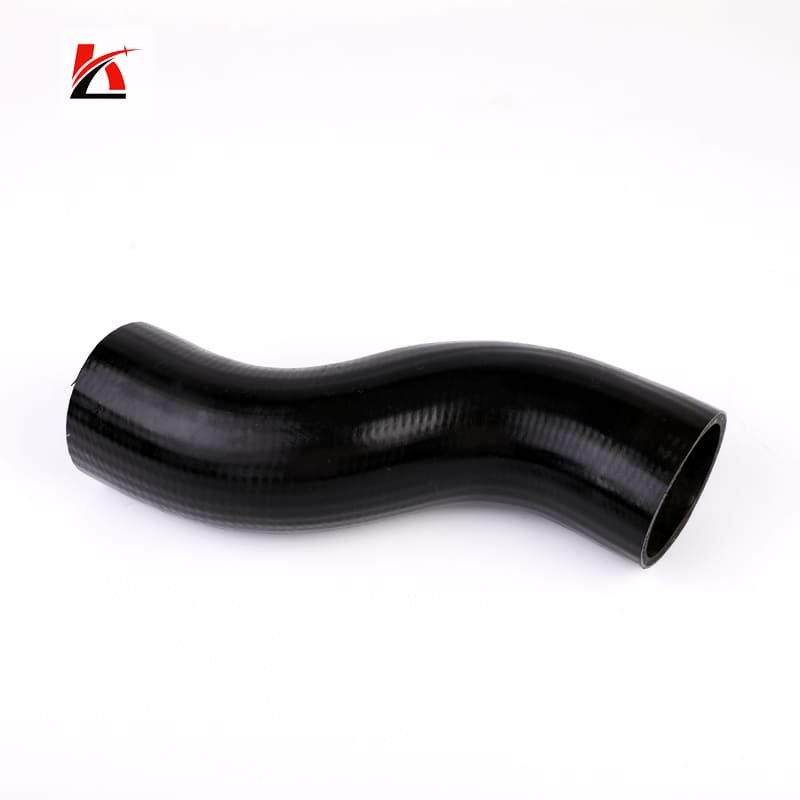
Rubber hoses are usually made from natural or synthetic rubber compounds like EPDM (ethylene propylene diene monomer) or SBR (styrene-butadiene rubber). These materials have good resistance to abrasion, weathering, and certain chemicals, which makes them suitable for a variety of applications.
Characteristics and Performance of Silicone Hoses
Silicone hoses are famous for being able to handle extreme heat, from -60°C to 280°C(-76+536°F ). They are super flexible, keep their shape over time, and don’t get old, don’t mind UV rays, and don’t mind ozone. This makes them perfect for high-performance and high-temperature applications.
Characteristics and Performance of Rubber Hoses
Rubber hoses are great at resisting abrasion, weathering, and certain chemicals. They can handle temperatures from -40°C to 180°C (-40°F to 356°F), which makes them perfect for a wide variety of general-purpose applications. However, rubber hoses may break down over time if they’re exposed to extreme temperatures or harsh environments.
Advantages and Disadvantages of Rubber Hoses Compared to Silicone Hoses
Advantages:
- 1. Cheaper
- 2. More oil and fuel-resistant
- 3. Good for low-temperature
Disadvantages:
- 1. Not as heat-resistant
- 2. More susceptible to aging and cracking
- 3. Less flexible over time
Advantages and Disadvantages of Silicone Hoses Compared to Rubber Hoses
Advantages:
- 1. Can withstand high temperatures
- 2. Lasts longer
- 3. Bends and keeps its shape well
Disadvantages:
- 1. More expensive
- 2. Poor compatibility with oil and fuel
- 3. Needs special clamps to keep it on
Silicone hose and rubber hose comparison table
Feature | Silicone hose | Rubber hose |
Material Composition | Made from silicone rubber, a polymer | Made from natural or synthetic rubber |
Temperature Resistance | High-temperature resistance (up to 350°F or higher) | Moderate temperature resistance (up to 212°F) |
Flexibility | Generally more durable, less prone to cracks | Can degrade faster under harsh conditions |
Cost | Generally more expensive | Less expensive |
Typical Applications | Automotive cooling systems, medical devices | Garden hoses, low-cost industrial applications |
Environmental Impact | More environmentally friendly, and less toxic when burned | Can release more toxic fumes, varies by type |
Color Variety | Available in various colors for aesthetic purposes | Typically limited to black or natural rubber color |
UV Resistance | Excellent UV resistance, does not degrade easily | Can degrade under prolonged UV exposure |
Vibration Damping | Better vibration damping capabilities vibration-damping | Less effective at vibration damping |
Performance in Ozone | High resistance to ozone and weathering | Prone to cracking and aging in ozone-rich areas |
Compression Set | Higher compression sets may lose shape over time | Higher compression sets may lose shape over time |
Applications of Silicone Hoses
Silicone hoses are great because they’re durable, flexible, and can withstand high temperatures. This makes them perfect for a bunch of different specialized uses across a bunch of different industries. Here are some of the common uses for silicone hoses:
1. Automotive and Aerospace Industries:
- (1). Cooling Systems: Silicone hoses are used for radiator and cooling system connections because they can handle high temperatures and are less likely to get hard or crack compared to rubber hoses.
- (2). Turbocharger Systems: They are often used in turbo systems where you need to be able to handle high temperatures and high pressure.
- (3). Air Intake Systems: Silicone hoses can handle the heat and reduce the risk of collapsing under pressure, so they work great for air intake connections.
2. Food and Beverage Industry:
- (1). Food Processing: Silicone hoses are used in food processing equipment because they can handle high temperatures and meet food safety standards.
- (2). Beverage Dispensing: They are used for beverage transfer when taste and odor neutrality are important.
3. Marine Applications:
- (1). Cooling and Heating Systems: Boats use silicone hoses to move coolant to and from engines and heating systems because they resist salt water and UV light.
4. Manufacturing and Industrial:
- (1). High-Temperature Environments: In industries where machines run hot, silicone hoses are used because they can handle the heat without breaking down.
- (2). Chemical Transfer: Silicone hoses are used for applications that involve moving mild chemicals because they don’t break down when they come into contact with chemicals.
5. Consumer Products:
- (1). Home Appliances: Silicone tubing is used in appliances like coffee makers and dishwashers, where resistance to heat and food-grade safety are important.
Silicone hoses are chosen for these applications because they offer a number of advantages over traditional rubber hoses. These include better performance in extreme temperatures, longer life, and lower maintenance.
Applications of Rubber Hoses
Rubber hoses are versatile and used across a broad range of applications due to their durability, flexibility, and resistance to wear. Here are some typical applications for rubber hoses:
1. Automotive Industry:
- (1). Coolant Hoses: Rubber hoses are used to move coolant between the radiator and the engine to control engine temperatures.
- (2). Fuel Lines: They deliver fuel from the tank to the engine and must be resistant to fuel and the additives found in modern fuels.
- (3). Air Intake Systems: Rubber hoses are used in air intake systems to connect air filters to the engine.
2. Construction and Mining:
- (1). Air Hoses: These are used to deliver air to pneumatic systems and tools.
- (2). Water Hoses: These are used to transport water to different parts of a construction or mining site.
- (3). Material Handling Hoses: These are designed to transport cement, sand, gravel, and other building materials.
3. Industrial Applications:
- (1). Irrigation Hoses: Big rubber hoses are used to spread water across fields.
- (2). Pesticide Spraying Hoses: Hoses that can handle all sorts of pesticides and other farm chemicals.
4. Oil and Gas Industry:
- (1). Oil transfer hoses: Used to offload and load oil from tankers, storage tanks, and oil transfer systems.
5. Marine Applications:
- (1). Marine Exhaust Hoses: Used to move engine exhaust gases on boats.
Rubber hoses are chosen for their ability to handle extreme conditions like high pressures, temperatures, and corrosive substances, making them suitable for harsh environments and demanding applications.
Are Silicone Hoses Better Than Rubber?
In conclusion, silicone hoses have many advantages over EPDM hoses. They can handle high temperatures, they last a long time, and they bend easily. That’s why people use them in industry and in cars.
What Are the Disadvantages of Silicone Hoses?
Silicone Sucks: Silicone doesn’t play well with oil, fuel, and other oil-based products. We don’t recommend using silicone hoses for any applications where they will come in contact with fuel or oil.
What Is the Benefit of Silicone Hoses?
Silicone hoses have many advantages that make them the top choice in many industries. They are heat resistant, flexible, durable, chemically resistant, insulating, work well in vacuum applications, and are easy to maintain.
When choosing between silicone and rubber hoses, consider the following factors:
1. Temperature Requirements
Silicone Hoses:
High Heat Resistance: Silicon hoses can handle extreme temperatures from -60°C to 280°C(-76+536°F ), making them perfect for high-performance applications like car engines and industrial machines that get really hot.
Consistency: They maintain their flexibility and structural integrity even at high temperatures, which means they’ll work when you need them to.
Rubber Hoses:
Moderate Temperature Range: Rubber hoses usually work fine from -40°C to 180°C (-40°F to 356°F). They work for most applications, but they may break down faster when exposed to higher temperatures.
Heat Damage: If you leave rubber hoses in the sun, they’ll get hard, crack, or lose their flexibility.
2. Exposure to Oils and Fuels
Silicone Hoses:
Not Good for Oil: Silicone hoses are not recommended for use with oil or fuel. The molecular structure of silicone makes it susceptible to swelling and degradation with exposure to oil and fuel. After the oil can use a Fluorosilicone hose.
Rubber Hoses:
Great Compatibility: Rubber hoses, especially those made from materials like EPDM or nitrile, are very resistant to oils, fuels, and other chemicals. They are often used in fuel lines, oil cooler lines, and other applications where they will be in contact with hydrocarbons.
3. Cost Constraints
Silicone Hoses:
More Expensive: Silicone hoses typically cost more than rubber hoses because of their better properties and the way they are made. This can be a big deal if you’re trying to do something on the cheap.
Rubber Hoses:
Cost-Effective: Rubber hoses are cheaper and provide a cost-effective solution for many general-purpose applications. They are often the preferred choice for large-scale projects where budget is a concern.
4. Durability and Longevity
Silicone Hoses:
Last a Long Time: Silicone hoses are tough and can withstand aging, UV rays, ozone, and environmental conditions. They tend to last longer than rubber hoses, which means you don’t have to replace them as often.
Resilience: They keep their properties over time, even in the face of adversity.
Rubber Hoses:
Medium Durability: Rubber hoses are good at resisting wear and tear, but they can break down faster if they’re exposed to extreme temperatures, UV rays, or ozone. You’ll need to check and maintain them regularly to make them last.
5. Flexibility and Shape Retention
Silicone Hoses:
Flexibility: Silicone hoses are extremely flexible and will not deform under pressure, even when bent or twisted. This makes them perfect for applications that require tight bends or complex routing.
Shape Memory: They return to their original shape after being stretched or compressed, so you can count on a great fit and performance.
Rubber Hoses:
Good Flexibility: Rubber hoses are also flexible but may become less pliable over time, especially under high heat or harsh environmental conditions. They may not hold their shape as well as silicone hoses in the long run.
6. Application-Specific Requirements
Silicone Hoses:
Specialized Uses: Thanks to their ability to withstand high temperatures and their durability, silicone hoses are often used in automotive performance parts, aerospace, and industrial machinery.
Performance Applications: Perfect for turbocharger systems, cooling systems, and other high-stress environments.
Rubber Hoses:
General Purpose: Rubber hoses are versatile and can be used in many different ways, like cars, factories, and homes.
Everyday Use: Used for fuel lines, air and water transfer, and other everyday applications.
Conclusion
When you’re deciding between silicone and rubber hoses, you need to think about what you’re going to use it for. You’ll need to know about temperature, oils and fuels, cost, how long it’s going to last, how flexible it is, and what you’re using it for. By knowing the pros and cons of each, you can make a better decision and get the right hose that will last a long time and work well for you.